- Pioneer Hydraulic Co., LTD
- Dension P080 series pump Rexroth piston pump A1VO (Series 10) Dension Gold cup P6P series pump
- Home
- Stock Categories
- Dension P080 series pump
- Rexroth piston pump A1VO (Series 10)
- Dension Gold cup P6P series pump
- Parker PVT64 series PUMP
- Dension Gold cup P8R series piston pump
- VICKERS Piston pump
- Dension Gold cup P11 pump
- Rexroth A11V series pump
- Rexroth pump (A)A4VSO (Series 10 & 30)
- Dension Gold cup P30 series pump
- Dension Gold cup P7R series piston pump
- Parker gear pump
- Rexroth Hydraulic Pump
- Parker PVT47 series PUMP
- Parker PVT10 PUMPS
- Rexroth pump A15VSO (Series 10)
- Rexroth piston pumps AA4VG (Series 32)
- Daikin VR Series Hydraulic Piston Pump
- Daikin RP Series Rotor Pump
- Japan Komatsu Hydraulic Pump
- Bosch Hydraulic Pump
- Dension P140 series pump
- Rexroth A10VSO Variable Axial Piston Pumps
- Eaton pumps
- Dension Gold cup P8P series pump
- T6CC vane pump
- Vickers pumps
- Rexroth AZPG series pump
- Parker pump PVV series
- Solenoid directional valves
- Rexroth A10VO Hydraulic Piston Pump
- Sauer Danfoss Pump
- Vickers vane pumps
- Rexroth piston pump A10V(S)O & (A)A10VSO (Series 31)
- Daikin V Series Hydraulic Piston Pump
- Parker PVT29 series Pump
- Dension Gold cup P8 pump
- Parker PVT38 series pump
- Fans cooling
- Dension Worldcup P8W series Pump
- Other Pump
- Daikin Hydraulic Vane Pumps
- REXROTH AA10VSO Variable Displacement Pumps
- Rexroth A10VO Pump
- Dension Worldcup P6W Pump
- operated directional valves
- Rexroth pumps AZPF and AZPN series
- Rexroth piston pumps
- Rexroth pumps
- Linde Hydraulic Pump
- Dension Gold cup P14 pump
- T6C T6D T6E T7E Single Vane Pump
- Daikin Hydraulic Pump
- Dension Worldcup P7W Pump
- Rexroth linear
- Rexroth PSV series Pump
- NACHI Hydraulic Pumps
- Vickers Hydraulic Pump
- Parker PVT6 series pump
- Parker PV series pump
- Dension P200 pump
- Hot sales Main pump
- Daikin VZ Series Hydraulic Piston Pump
- Rexroth A10VSO Variable Axial Piston Pump
- Dension Gold cup P7 pump
- Rexroth Piston pump AA10VG (Series 10)
- Dension Gold cup P24 pump
- Rexroth valve
- Check valves
- Sumitomo Hydraulic Internal Gear Pump
- pressure swithes
- Mitsubishi Motor
- filteration filter elements
- Denison Hydraulic Pumps
- Japan Yuken Hydraulic Pump
- REXROTH AA10VSO Variable Displacement Pump
- Dension Gold cup P7P series pump
- Yuken accessories
- TDY Italy piston motors
- PARKER PVT20 PUMP
- Rexroth PGH series gear pump
- Rexroth A10VO Hydraulic Piston Pumps
- Any gear pumps
- Rexroth piston pumps A10V(S)O (Series 52)
- Parker PV7 - Direct Operated
- Parker VPV series pump
- Any vane pumps
- Dension P260Q series pump
- Rexroth pressure valves
- Rexroth pumps A10VSO (Series 32)
- Hitachi Hydraulic Pump
- Dension P110 pump
- relief valves
- Control valves
- Dension Gold cup P6 pump
- Dension Gold cup P6R series piston pump
- Parker PVT15 Pumps
- Japanese Sumitomo QT4223 Series Double Gear Pump
- Japanese Sumitomo QT5143 Series Double Gear Pump
- Japanese Sumitomo QT4222 Series Double Gear Pump
- Japanese Sumitomo QT5252 Series Double Gear Pump
- Japanese Sumitomo QT52 Series Gear Pump
- Japanese Sumitomo QT3223 Series Double Gear Pump
- Japanese Sumitomo QT41 Series Gear Pump
- Japanese Sumitomo QT33 Series Gear Pump
- Japanese Sumitomo QT6123 Series Double Gear Pump
- Japanese Sumitomo QT4322 Series Double Gear Pump
- Japanese Sumitomo QT5333 Series Double Gear Pump
- Japanese Sumitomo QT2222 Series Double Gear pump
- Japanese Sumitomo QT5223 Series Double Gear Pump
- Japanese Sumitomo QT6252 Series Double Gear Pump
- Japanese Sumitomo QT32 Series Gear Pump
- Japanese Sumitomo QT51 Series Gear Pump
- Japanese Sumitomo QT4323 Series Double Gear Pump
- Japanese Sumitomo QT62 Series Gear Pump
- Japanese Sumitomo QT4232 Series Double Gear Pump
- Japanese Sumitomo QT2323 Series Double Gear pump
- Japanese Sumitomo QT4123 Series Double Gear Pump
- Japanese Sumitomo QT6262 Series Double Gear Pump
- Japanese Sumitomo QT5242 Series Double Gear Pump
- Japanese Sumitomo QT4242 Series Double Gear Pump
- Japanese Sumitomo QT61 Series Gear Pump
- Japanese Sumitomo QT5133 Series Double Gear Pump
- Japanese Sumitomo QT43 Series Gear Pump
- Japanese Sumitomo QT4233 Series Double Gear Pump
- Japanese Sumitomo QT6153 Series Double Gear Pump
- Japanese Sumitomo QT5243 Series Double Gear Pump
- Japanese Sumitomo QT6253 Series Double Gear Pump
- Japanese Sumitomo QT53 Series Gear Pump
- Japanese Sumitomo QT63 Series Gear Pump
- Japanese Sumitomo QT23 Series Gear Pump
- Japanese Sumitomo QT22 Series Gear Pump
- Japanese Sumitomo QT31 Series Gear Pump
- Japanese Sumitomo QT3222 Series Double Gear Pump
- Japanese Sumitomo QT6143 Series Double Gear Pump
- Japanese Sumitomo QT6222 Series Double Gear Pump
- Japanese Sumitomo QT42 Series Gear Pump
- Denso Injector Nozzle
- Common Rail Nozzle
- Fuel Injector Nozzle
- Bosch Injector Nozzles
- Dension Vane pump T6 series
- Dension Vane pump SDV series
- Daikin Hydraulic Piston Pump V series
- Dension Piston pump P7 series
- Dension Piston pump P series
- Daikin Hydraulic Piston Pump VZ series
- Dension Vane pump T7 series
- Parker Piston pump PV020 series
- Dension Piston pumps P6 series
- Daikin Hydraulic Piston Pump VR series
- Vickers Variable piston pumps PVH Series
- Vickers Variable piston pumps PVB Series
- Original Rexroth AZPGG series Gear Pump
- Original Rexroth A10VO Series Piston Pump
- Original Rexroth A10VSO Series Piston Pump
- Original Rexroth AA10VSO Series Piston Pump
- Original Rexroth AZPGF series Gear Pump
- Original Rexroth A4VSO Series Piston Pump
- Sauer-Danfoss Piston Pumps
- Original hydraulic pump
- HYDRAULIC PISTON PUMP
- Original Pump
- Hydraulic Pump
- Needle Roller Bearings
- Angular Contact Ball Bearings
- Quality Control
- Dension P080 series pump
- Rexroth piston pump A1VO (Series 10)
- Dension Gold cup P6P series pump

Home> Company News> What are the suggested procedures for TIMKEN bearing analysis?
- Product Groups
Dension P080 series pump
(2306)Rexroth piston pump A1VO (Series 10)
(25)Dension Gold cup P6P series pump
(482)Parker PVT64 series PUMP
(1)Dension Gold cup P8R series piston pump
(162)VICKERS Piston pump
(586)Dension Gold cup P11 pump
(2085)Rexroth A11V series pump
(31)Rexroth pump (A)A4VSO (Series 10 & 30)
(11)Dension Gold cup P30 series pump
(1446)Dension Gold cup P7R series piston pump
(162)Parker gear pump
(13)Rexroth Hydraulic Pump
(7197)Parker PVT47 series PUMP
(562)Parker PVT10 PUMPS
(769)Rexroth pump A15VSO (Series 10)
(23)Rexroth piston pumps AA4VG (Series 32)
(32)Daikin VR Series Hydraulic Piston Pump
(28)Daikin RP Series Rotor Pump
(218)Japan Komatsu Hydraulic Pump
(3374)Bosch Hydraulic Pump
(8248)Dension P140 series pump
(2306)Rexroth A10VSO Variable Axial Piston Pumps
(1608)Eaton pumps
(1300)Dension Gold cup P8P series pump
(482)T6CC vane pump
(91)Vickers pumps
(115)Rexroth AZPG series pump
(12)Parker pump PVV series
(16)Solenoid directional valves
(1143)Rexroth A10VO Hydraulic Piston Pump
(1005)Sauer Danfoss Pump
(1224)Vickers vane pumps
(60)Rexroth piston pump A10V(S)O & (A)A10VSO (Series 31)
(82)Daikin V Series Hydraulic Piston Pump
(812)Parker PVT29 series Pump
(770)Dension Gold cup P8 pump
(323)Parker PVT38 series pump
(562)Fans cooling
(190)Dension Worldcup P8W series Pump
(661)Other Pump
(95)Daikin Hydraulic Vane Pumps
(86)REXROTH AA10VSO Variable Displacement Pumps
(82)Rexroth A10VO Pump
(358)Dension Worldcup P6W Pump
(1190)operated directional valves
(232)Rexroth pumps AZPF and AZPN series
(73)Rexroth piston pumps
(3000)Rexroth pumps
(5695)Linde Hydraulic Pump
(8015)Dension Gold cup P14 pump
(874)T6C T6D T6E T7E Single Vane Pump
(3500)Daikin Hydraulic Pump
(973)Dension Worldcup P7W Pump
(1190)Rexroth linear
(592)Rexroth PSV series Pump
(36)NACHI Hydraulic Pumps
(497)Vickers Hydraulic Pump
(10868)Parker PVT6 series pump
(769)Parker PV series pump
(401)Dension P200 pump
(2306)Hot sales Main pump
(1266)Daikin VZ Series Hydraulic Piston Pump
(244)Rexroth A10VSO Variable Axial Piston Pump
(1864)Dension Gold cup P7 pump
(323)Rexroth Piston pump AA10VG (Series 10)
(14)Dension Gold cup P24 pump
(1449)Rexroth valve
(3930)Check valves
(125)Sumitomo Hydraulic Internal Gear Pump
(1113)pressure swithes
(30)Mitsubishi Motor
(535)filteration filter elements
(810)Denison Hydraulic Pumps
(267)Japan Yuken Hydraulic Pump
(490)REXROTH AA10VSO Variable Displacement Pump
(422)Dension Gold cup P7P series pump
(482)Yuken accessories
(84)TDY Italy piston motors
(90)PARKER PVT20 PUMP
(771)Rexroth PGH series gear pump
(32)Rexroth A10VO Hydraulic Piston Pumps
(1000)Any gear pumps
(330)Rexroth piston pumps A10V(S)O (Series 52)
(145)Parker PV7 - Direct Operated
(11)Parker VPV series pump
(41)Any vane pumps
(1335)Dension P260Q series pump
(787)Rexroth pressure valves
(106)Rexroth pumps A10VSO (Series 32)
(9)Hitachi Hydraulic Pump
(5050)Dension P110 pump
(2306)relief valves
(743)Control valves
(421)Dension Gold cup P6 pump
(323)Dension Gold cup P6R series piston pump
(162)Parker PVT15 Pumps
(1538)Japanese Sumitomo QT4223 Series Double Gear Pump
(14)Japanese Sumitomo QT5143 Series Double Gear Pump
(10)Japanese Sumitomo QT4222 Series Double Gear Pump
(15)Japanese Sumitomo QT5252 Series Double Gear Pump
(4)Japanese Sumitomo QT52 Series Gear Pump
(18)Japanese Sumitomo QT3223 Series Double Gear Pump
(13)Japanese Sumitomo QT41 Series Gear Pump
(13)Japanese Sumitomo QT33 Series Gear Pump
(13)Japanese Sumitomo QT6123 Series Double Gear Pump
(13)Japanese Sumitomo QT4322 Series Double Gear Pump
(9)Japanese Sumitomo QT5333 Series Double Gear Pump
(10)Japanese Sumitomo QT2222 Series Double Gear pump
(11)Japanese Sumitomo QT5223 Series Double Gear Pump
(13)Japanese Sumitomo QT6252 Series Double Gear Pump
(5)Japanese Sumitomo QT32 Series Gear Pump
(13)Japanese Sumitomo QT51 Series Gear Pump
(17)Japanese Sumitomo QT4323 Series Double Gear Pump
(4)Japanese Sumitomo QT62 Series Gear Pump
(22)Japanese Sumitomo QT4232 Series Double Gear Pump
(10)Japanese Sumitomo QT2323 Series Double Gear pump
(7)Japanese Sumitomo QT4123 Series Double Gear Pump
(13)Japanese Sumitomo QT6262 Series Double Gear Pump
(6)Japanese Sumitomo QT5242 Series Double Gear Pump
(10)Japanese Sumitomo QT4242 Series Double Gear Pump
(6)Japanese Sumitomo QT61 Series Gear Pump
(10)Japanese Sumitomo QT5133 Series Double Gear Pump
(10)Japanese Sumitomo QT43 Series Gear Pump
(13)Japanese Sumitomo QT4233 Series Double Gear Pump
(10)Japanese Sumitomo QT6153 Series Double Gear Pump
(10)Japanese Sumitomo QT5243 Series Double Gear Pump
(11)Japanese Sumitomo QT6253 Series Double Gear Pump
(10)Japanese Sumitomo QT53 Series Gear Pump
(13)Japanese Sumitomo QT63 Series Gear Pump
(13)Japanese Sumitomo QT23 Series Gear Pump
(16)Japanese Sumitomo QT22 Series Gear Pump
(16)Japanese Sumitomo QT31 Series Gear Pump
(13)Japanese Sumitomo QT3222 Series Double Gear Pump
(16)Japanese Sumitomo QT6143 Series Double Gear Pump
(10)Japanese Sumitomo QT6222 Series Double Gear Pump
(13)Japanese Sumitomo QT42 Series Gear Pump
(19)Denso Injector Nozzle
(580)Common Rail Nozzle
(217)Fuel Injector Nozzle
(285)Bosch Injector Nozzles
(170)Dension Vane pump T6 series
(1303)Dension Vane pump SDV series
(373)Daikin Hydraulic Piston Pump V series
(813)Dension Piston pump P7 series
(569)Dension Piston pump P series
(1203)Daikin Hydraulic Piston Pump VZ series
(246)Dension Vane pump T7 series
(528)Parker Piston pump PV020 series
(612)Dension Piston pumps P6 series
(531)Daikin Hydraulic Piston Pump VR series
(25)Vickers Variable piston pumps PVH Series
(1891)Vickers Variable piston pumps PVB Series
(371)Original Rexroth AZPGG series Gear Pump
(170)Original Rexroth A10VO Series Piston Pump
(1000)Original Rexroth A10VSO Series Piston Pump
(1864)Original Rexroth AA10VSO Series Piston Pump
(423)Original Rexroth AZPGF series Gear Pump
(157)Original Rexroth A4VSO Series Piston Pump
(1368)Sauer-Danfoss Piston Pumps
(763)Original hydraulic pump
(10)HYDRAULIC PISTON PUMP
(16)Original Pump
(13)Hydraulic Pump
(14)Needle Roller Bearings
(57)Angular Contact Ball Bearings
(58)
- AddressNo.9088 SHAHEXI ROAD, NANSHAN DISTRICT,SHENZHEN,CHINA
- Factory AddressNo.9088 SHAHEXI ROAD, NANSHAN DISTRICT,SHENZHEN,CHINA
- Worktime9:00-18:00
- Phone(Working Time)0531-85064681
- Phone(Nonworking Time)0531-85064681
- Fax0531-85064681
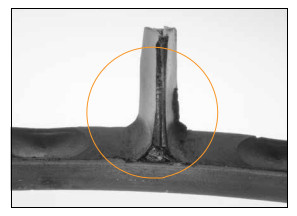
Follow the steps below for an accurate and complete analysis when investigating any bearing damage or system breakdowns. If you need help, contact some of our sales or service engineers.
1. Gather operating data from bearing monitoring devices; analyze service and maintenance records and charts; and secure application diagrams, graphics or engineering drawings.
2. Prepare an inspection sheet to capture all your observations. Take photographs throughout the procedure to help document or describe the damaged components.
3. Extract any used lubricant samples from bearings, housing and seal areas to determine lubricant conditions. Package it separately and label it properly.
4. Secure a sample of new, unused lubricant. Record any specification or batch information from the container. Obtain the technical specifications and any related material safety data (handling, disposal, toxicological) documentation to accompany lubricant shipments.
5. Check the bearing environment for external influences, like other equipment problems, that preceded or occurred at the same time bearing damage was reported.
6. Disassemble the equipment (either partially or completely). Record an assessment of the mounted bearing condition.
7. Inspect other machine elements, especially the position and condition of components adjacent to the bearing, including locknuts, adapters, seals and seal wear rings.

8. Mark and record the mounted position of the bearings and components until removal.
9. Measure and verify shaft and housing size, roundness and taper using certified gauges.
10. Following removal, but before cleaning, record observations of lubricant distribution and condition.
11. Clean parts and record the manufacturers' information from markings on the bearing rings (part number, identification number,
date code).
12. Analyze the condition of the internal rolling contact surfaces, load zones and the corresponding external surfaces.
13. Apply preservative oil and repackage the bearings to avoid corrosion.
14. Compile a summary report of all data for discussion with Timken sales or service engineers.r service engineers.
- Previous pageHow are the TIMKEN bearings set up?
- Next pageWhich bearings and rod ends of SKF need to be maintained?